GOOSENECK – O&G INDUSTRY
Hazelett Drilling, Inc. required a more efficient, longer wearing gooseneck for their drilling operations.
Read More
CUSTOMER |
|
Hazelett Drilling Company 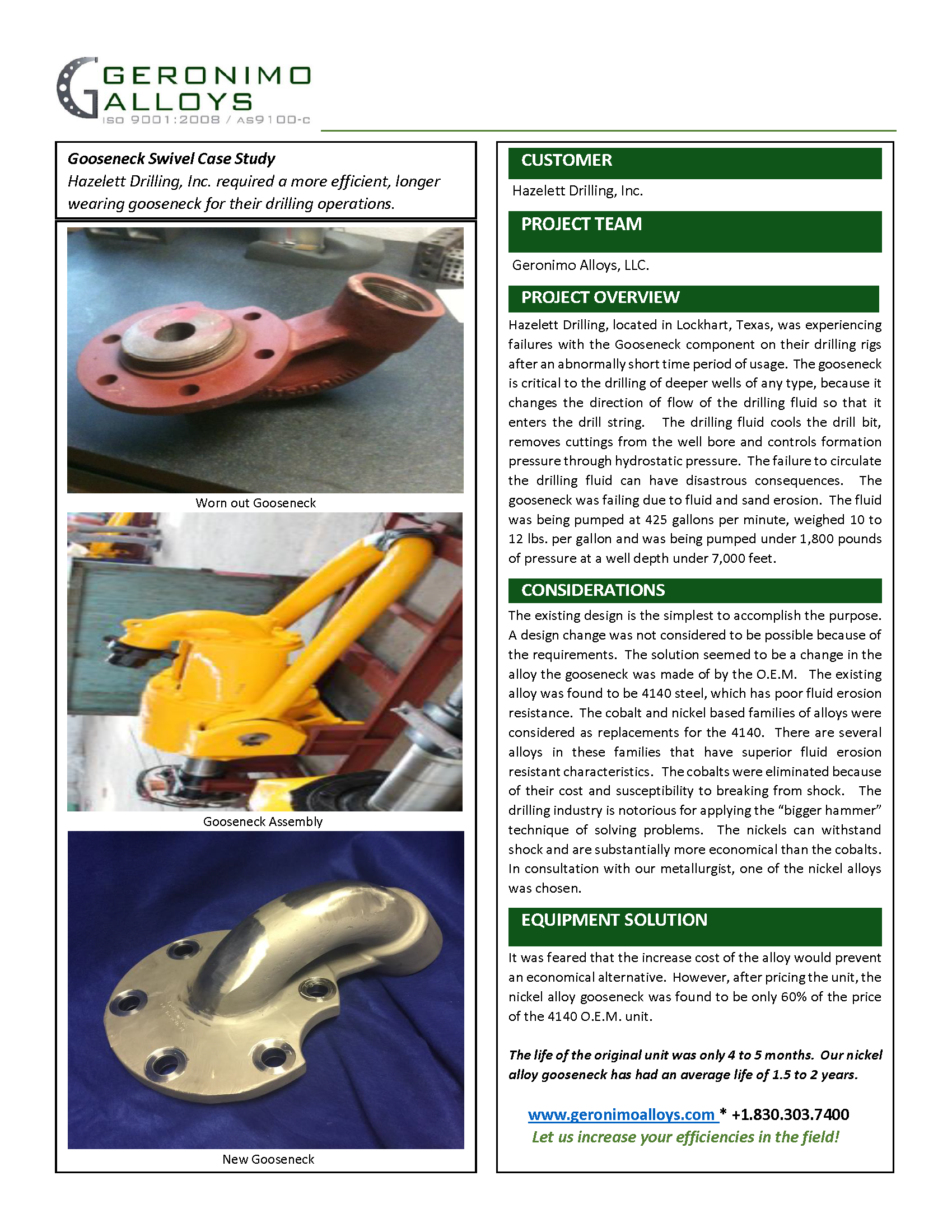 |
LEAF CHOKE – POLYMER INDUSTRY
Simple, Scalable Pressure Control Device
Read More
CUSTOMER |
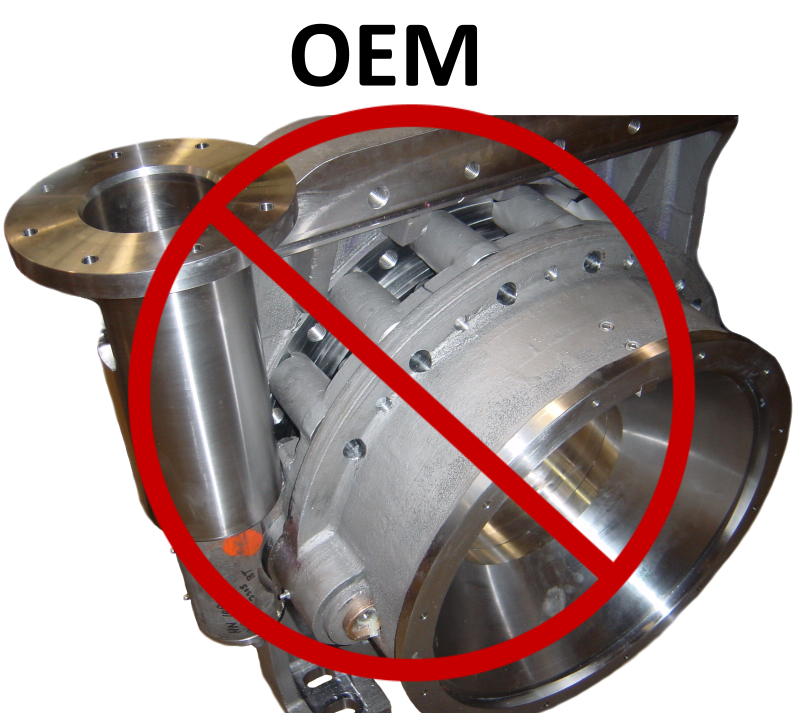 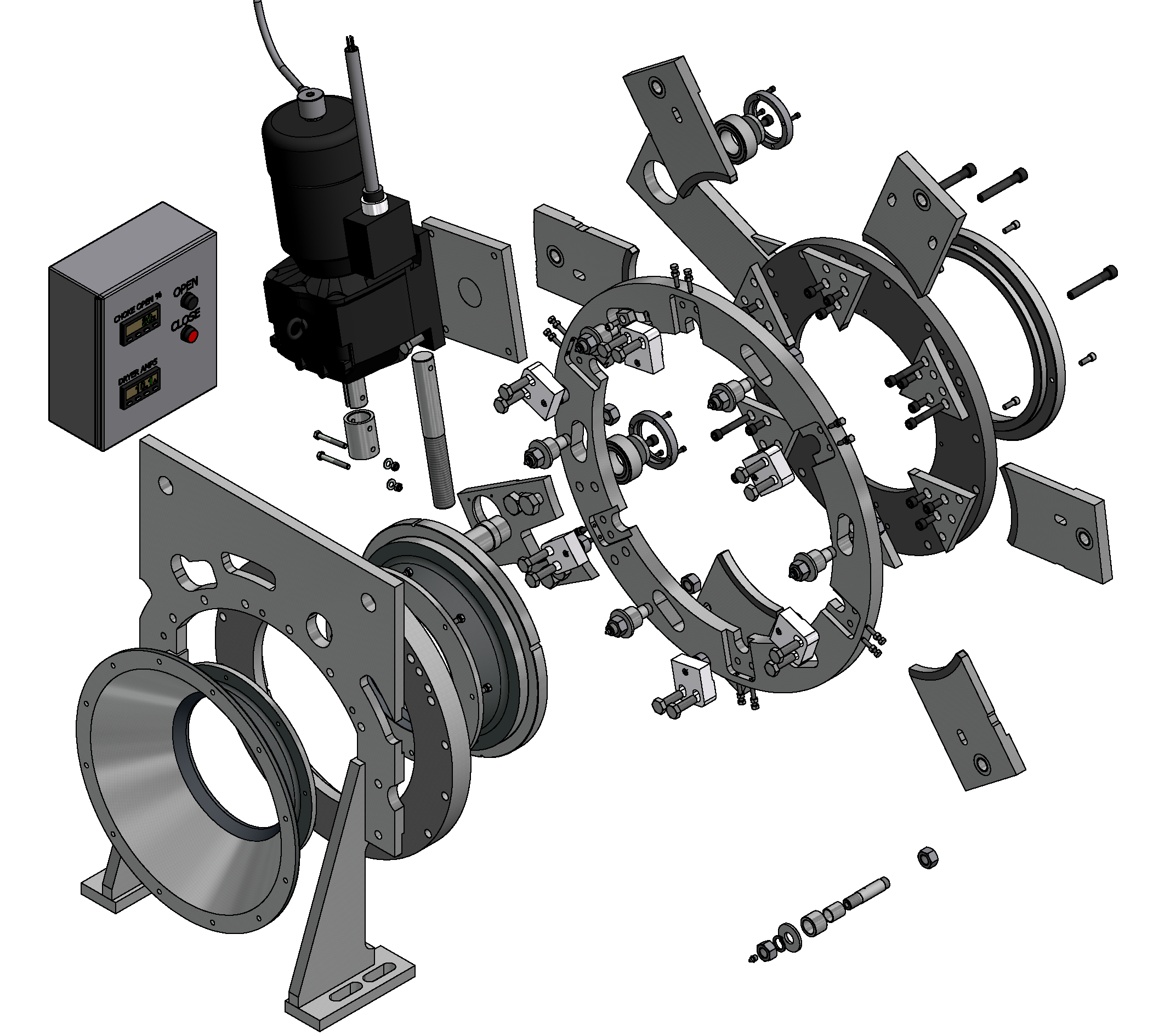 |
Polymer Manufacturing Company |
PROJECT TEAM
|
Geronimo Alloys, LLC. |
PROJECT OVERVIEW |
The existing pressure control device or choke offered by the O.E.M. was expensive and unnecessarily complicated. The device varied the open area at the end of a polymer dryer to control the pressure exerted in the dryer which, in turn, controlled the amount of moisture remaining in the product. The original equipment had to be operated with a motor and contained various gears too move the cone that created the opening. The goal of the new device was to simplify the movement and, yet, allow the method of movement to be variable from very simple to remotely controllable.
The new design eliminated the gears, motor, and wear cone. A simple cam mechanism allowed the leaves of the iris to move in and out to vary the opening. The inside of the leaves created a circle that when opened created the same greatest opening of the original choke and when closed the same minor opening. There was no change in the shaft piece that created the other side of the opening. A stationary arm and a rotating arm created the movement. The arms can be moved with a variety of mechanisms. Some companies use a device as simple as a turnbuckle or a hydraulic cylinder. One company desired to operate the choke from a control room, so a motor was added and remote operating was included in the control. PLC control allowed the choke to vary the opening depending on a variety of conditions that existed in the machine. Pressure or temperature were two variables that could automatically vary the choke opening.
|
CONSIDERATIONS |
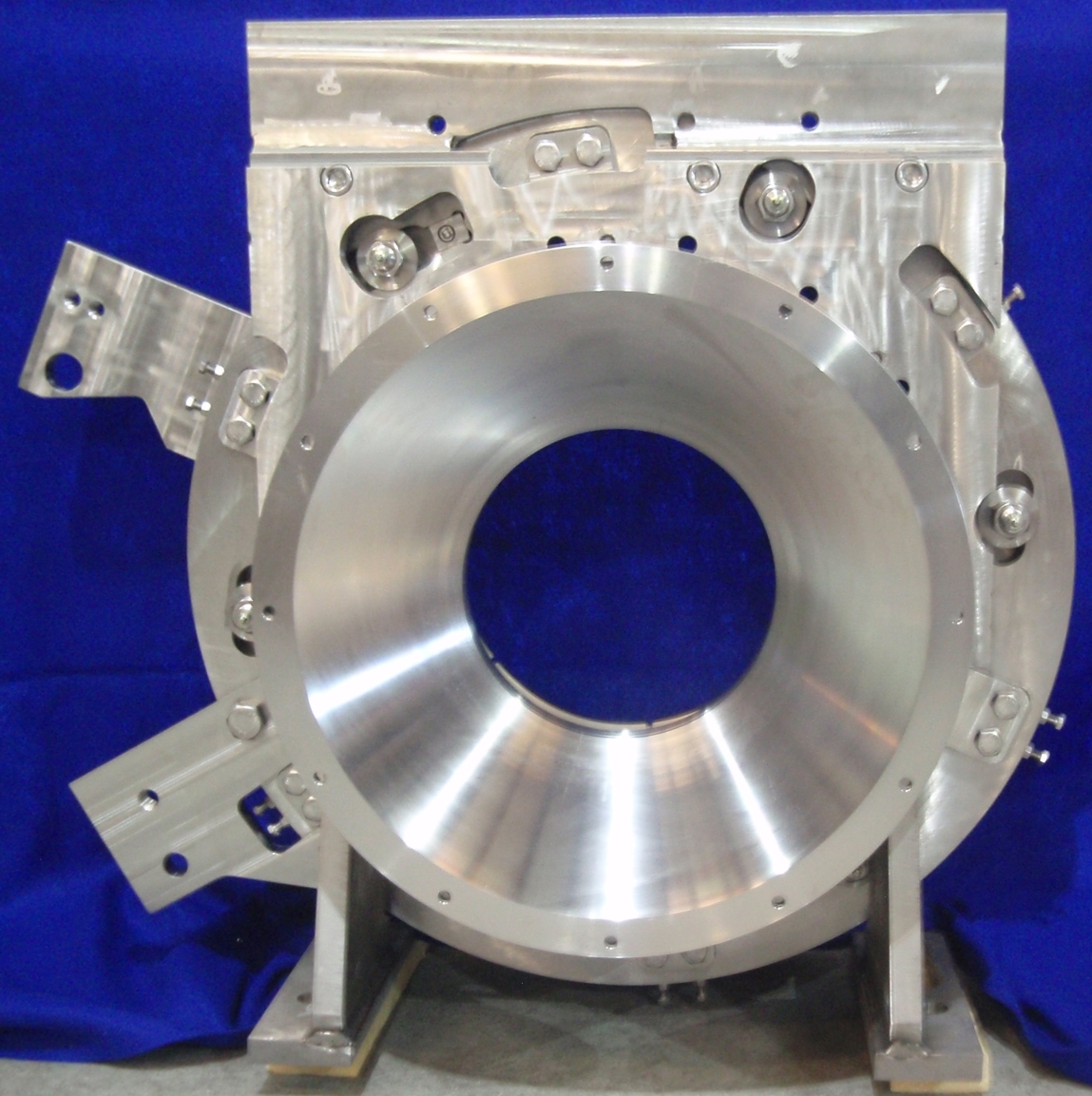 |
The newly designed choke had been simplified to the extent that it was 18 inches shorter than the original equipment. The space was filled by a separate discharge device so that the polymer company did not have to re-arrange their production layout. The attachment to the dryer was designed to interchange with the original equipment. |
EQUIPMENT SOLUTION |
The Iris or Leaf choke resulted in a much less expensive device to manufacture. The original device had a long list of wear parts that would need replacing. They included motor, gears, and cone. The cost of a total replacement was more than $20,000. The most common wear part was the choke cone and the cost to replace it was more than $12,000. The Leaf Choke, without a motor, only had the wear edge of the leafs that needed replacing. The leaves were designed to be repairable so the cost to repair was only $1,800. This is a savings of $10,200 over a cone replacement.
The new Leaf choke resulted in a simpler device that was scalable to meet the operator’s requirements. It is approximately 60% of the cost of the O.E.M. equipment. The replacement cost of the wear parts is 15% of the O.E.M. choke. |
SUPER BOWL – REFINING INDUSTRY
An oil refinery went down as a critical valve part failed.
Read More
PLASTICS INDUSTRY
Higher Quality with Timely Delivery vs. OEM
Read More
CUSTOMER |
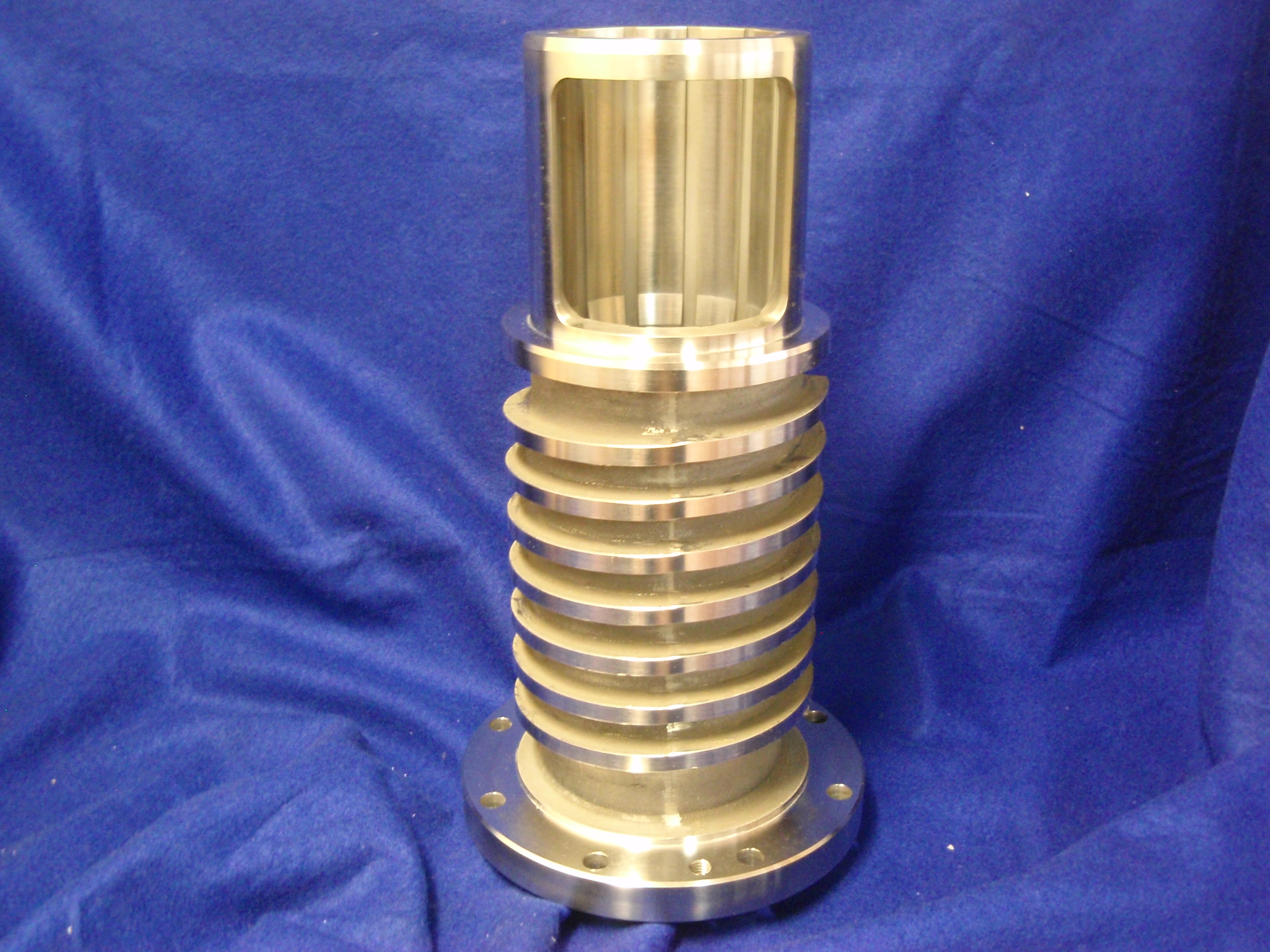 |
Manufacturer of Outdoor Equipment |
PROJECT TEAM
|
Geronimo Alloys, LLC. |
PROJECT OVERVIEW |
Our customer, with whom we have done business for many years, is one of the largest manufacturers of polymer/plastic based coolers and various outdoor products in the world. Their manufacturing machines and facilities require the highest quality replacement/wear parts, so that they can minimize their downtime, while continuing their manufacturing process 24/7/365.
Prior to beginning to manufacture their parts, they came to us
looking for a solution to their problem of unacceptable
manufacturing times from the O.E.M., combined with the quality of the parts, so that their operations would not be unnecessarily delayed, thereby decreasing their output and corresponding revenues.
As a result, we have enjoyed manufacturing their requisite
replacement/wear parts by designing, casting, pouring and
machining the same for many years. Our in-house foundry,
combined with an extensive machine shop, provides us with
advantages that many other manufactures desire. Our solution not only continues to save them time and money, but provides them with a competitive advantage in the market place.
|
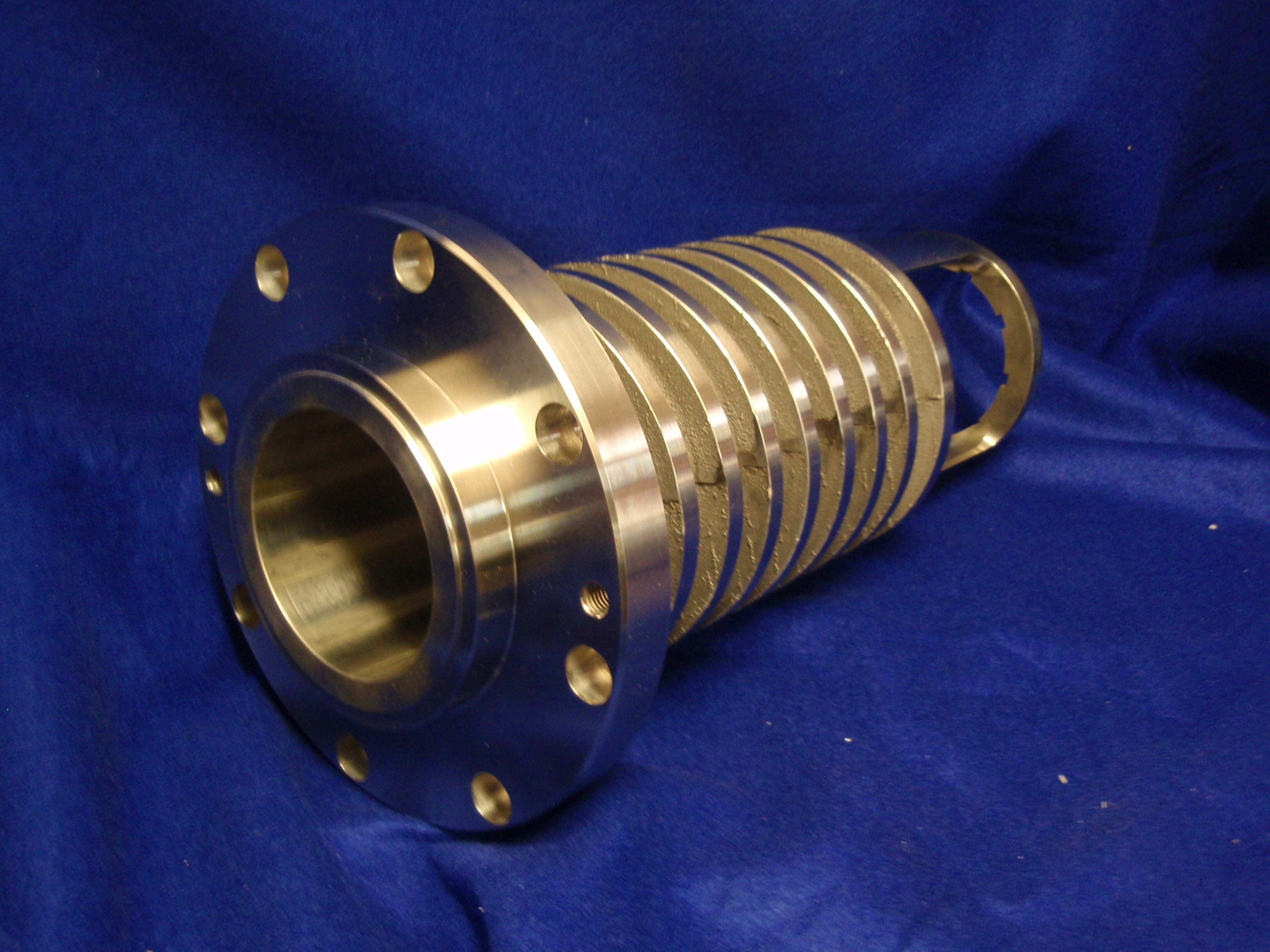 |
CONSIDERATIONS |
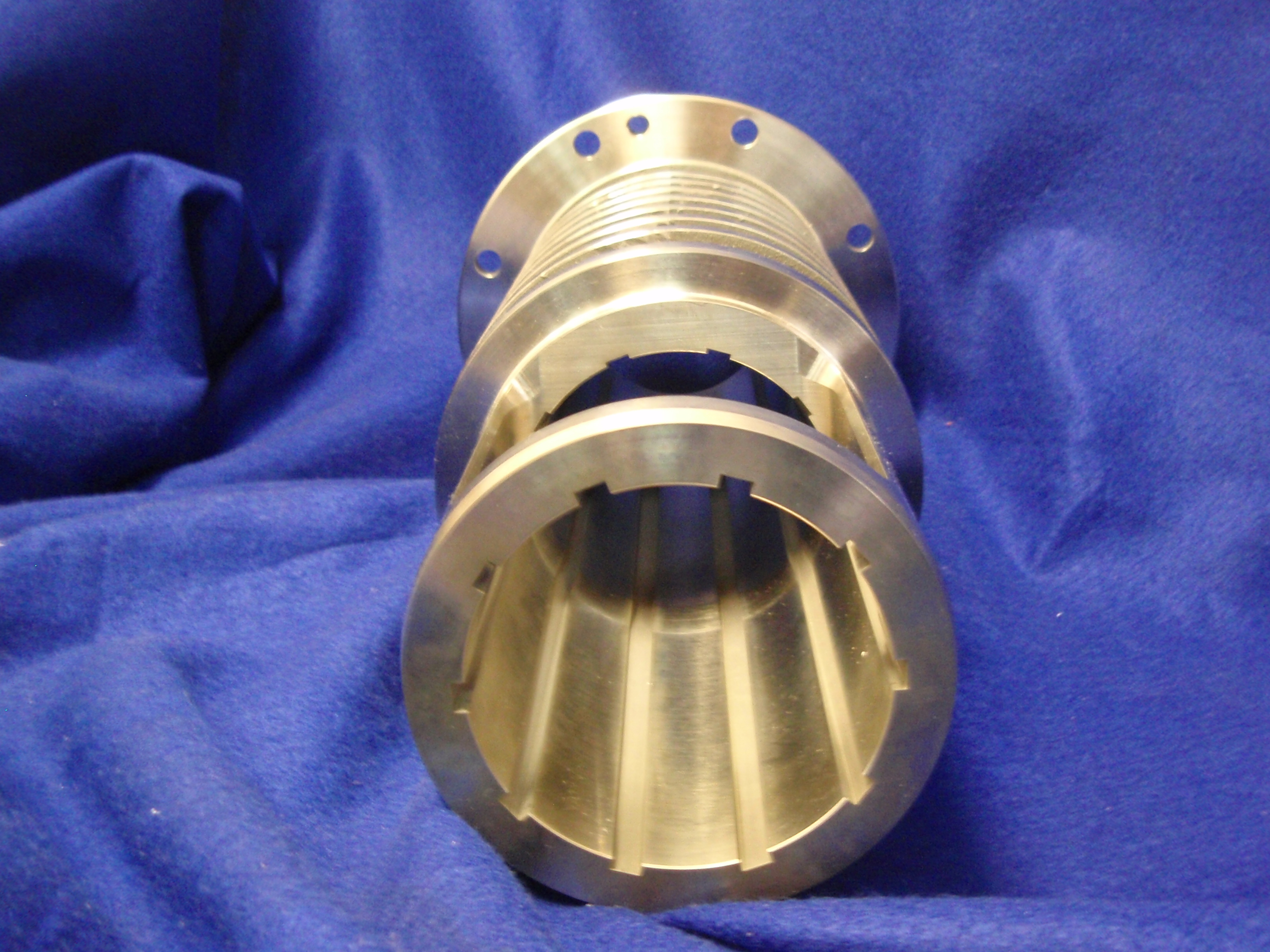 |
Environmental conditions, including varying degrees of heat, various chemical impact and ease of replacement by maintenance staff were critical in determining the best solution. |
EQUIPMENT SOLUTION |
Over the years, we have manufactured the following parts:
60 mm feed zone bushing;
70 mm feed zone bushing;
80 mm feed zone bushing;
90 mm feed zone bushing;
100 mm feed zone bushing.
Currently, we are in the process of evaluating additional parts to manufacture for them, thereby further enhancing their process efficiencies. Our parts continue to add a more cost effective solution for their processes, which has in turn made them more mechanically efficient and economically viable.
|
|